AI-Designed Enzyme Eats Plastic
It's the fastest enzyme yet, but the technology is still a long way from transforming the planet.
A plastic-eating enzyme can break down polyethylene terephthalate (PET), the same plastic used to make water bottles and textiles, at rates that vastly exceed prior reports. The results were published today in Nature.
The engineered enzyme, called FAST PETase, breaks down a pre-melted water bottle in a little under two weeks at an incubation temperature of 50°C. That might seem slow, but it’s more than three times faster than any other PET-degrading enzyme at that temperature. Two other PET-degrading enzymes can operate at similar efficiencies, but only at higher temperatures (around 70°C).
PET plastic is used to create single-use bottles, bags, clothes and textiles. About 12 percent of all solid waste on planet Earth is made from plastic.
A bacterium called Ideonella sakaiensis eats PET in the wild, breaking down the plastic and using it as a carbon source. That evolutionary quirk was first reported in Science in 2016. But chemists have been making and using PET-degrading enzymes for far longer, since at least 2005.
FAST PETase was designed using a freely available convolutional neural network, called MutCompute, that predicts which amino acid “swaps” will stabilize a protein. The engineered enzyme differs in just six different amino acids compared with the wildtype enzyme from Ideonella sakaiensis.
This paper is exciting, and I’m sure it will get cited a lot. (A 2020 paper, also in Nature, reported an engineered PETase that could break down plastic slightly faster than natural enzymes; it's been cited 419 times and has been downloaded 65,000 times.) But even if this enzyme was scaled massively, and plastic was degraded in giant vats, it would take an obscene number of years to remove all the PET plastic that humans generate in a single year (which is roughly equal in weight to 255 Empire State buildings). More on that later.
The study was led by Hongyuan Lu, a postdoctoral scholar in Hal Alper’s group at the University of Texas at Austin.
Nature’s Scaffold
There have been at least two notable efforts to ‘supercharge’ the PETase enzyme from I. sakaiensis by swapping in new amino acids at key positions. ThermoPETase and DuraPETase, the results of those efforts, both have increased PET-degrading activity compared with wildtype enzyme.
In this study, Alper’s team started by taking wildtype PETase, ThermoPETase and DuraPETase and feeding each protein sequence into the MutCompute algorithm, which predicts “positions within a protein in which wild-type amino acids are not optimized for their local environments.” The researchers basically performed an in silico mutagenesis screen; they computationally predicted, at every amino acid position, whether a different amino acid would make the protein more stable and, thus, more active at lower temperatures.
Protein mutants with the “best scores,” as determined by MutCompute, were artificially synthesized in the lab. Their enzymatic activities were measured. A variant of ThermoPETase with just three swapped amino acids — N233K, R224Q and S121E — had 38-fold higher activity at 50°C, relative to the original enzyme. This redesigned enzyme was dubbed “FAST PETase.”
Enter the Real World
PET is one chemical, but plastic products vary widely; in thickness and crystallinity, in shape and size. (Crystallinity is a measure of a polymer’s structure; higher crystallinity implies a more regular alignment of monomers.) To benchmark FAST PETase, 51 different plastic products were gathered up in the lab. A little hole was punched out from each one. Each “plastic hole” was then submerged in a liquid with the FAST PETase enzyme.
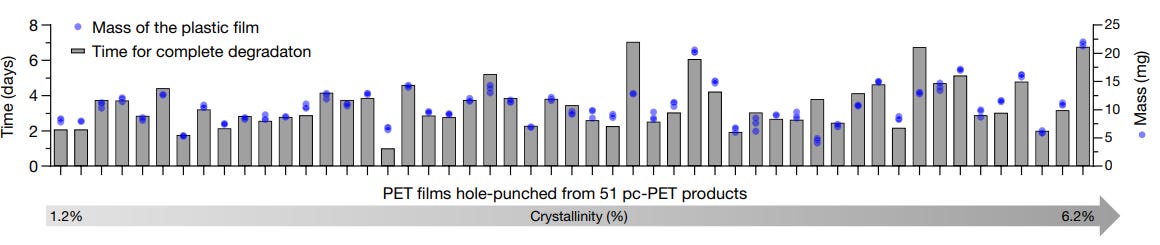
Regardless of the plastic’s mass and crystallinity, FAST-PETase fully degraded each plastic piece within one week at 50°C.
In another experiment, FAST PETase was scaled up and tested on a “large, untreated” piece of plastic that weighed 6.4 grams (a mass equivalent to about two-and-a-half U.S. pennies). It took about two days for the enzymes to fully degrade the plastic.
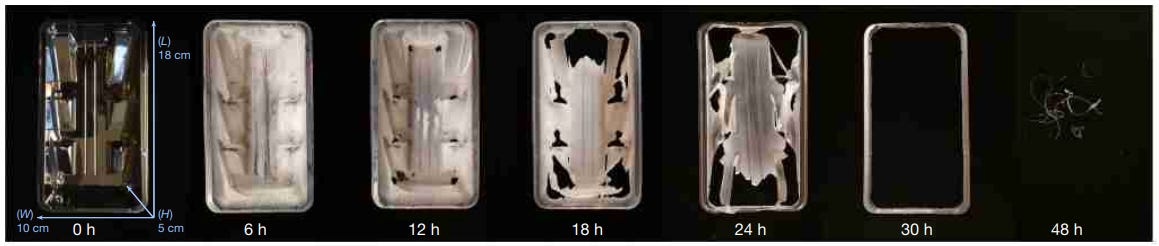
Bottleneck
FAST PETase has a major problem. The time that it takes this enzyme to break down a piece of plastic scales linearly with the plastic’s mass. It does not scale linearly with the plastic’s crystallinity.
Consider a single water bottle: The neck is built from PET plastics with a low crystallinity (about 1 percent), whereas the bottle’s body has a much higher crystallinity (20-30 percent) — the enzyme struggles to degrade the latter.
FAST PETase, in fact, cannot degrade untreated water bottles at all. Each bottle must first be melted down to form a plastic puck with uniform crystallinity. And, even then, it takes two weeks to fully degrade a single, melted, plastic bottle.
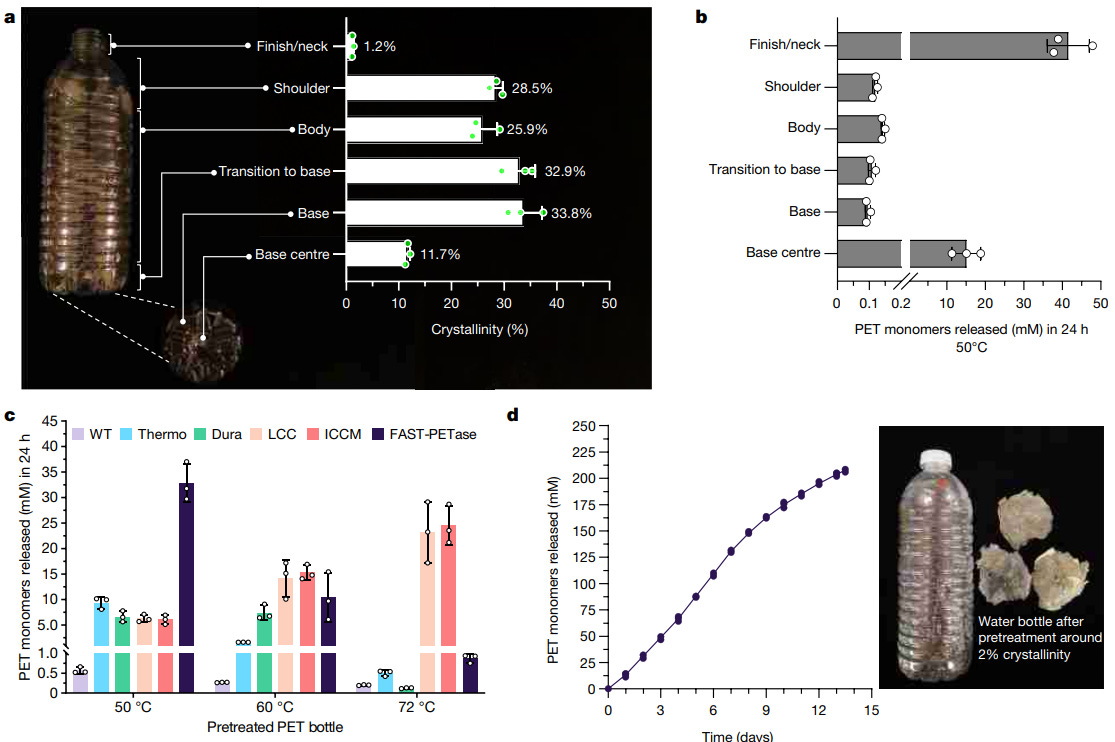
Compared to prior versions of PETase enzymes, however, FAST PETase performs far better at lower temperatures. At 50°C, the enzyme releases nearly 35 mM of PET monomers every 24 hours. That’s more than three times faster than any other enzyme at that temperature, but only slightly faster than enzymes optimized to operate at higher temperatures.
Operating at a lower temperature is so crucial, though, because if this process is ever scaled up — and I hope it will be — the energy cost savings will be massive.
Caveats
More than 82 million metric tons of PET plastics are produced each year. That's 180,777,200,000 pounds of plastic (if you're American), or roughly equivalent in weight to 225 Empire State Buildings.
It is because of the obscene scale of this problem that this new study offers hope — you will almost certainly see articles in the news today touting this paper as some transformative stepping stone towards cleaning up our planet’s junk. And yes, it is a big improvement, but only when compared to its horrendously slow predecessors.
In the final experiment from this paper, the enzyme broke down a single plastic bottle, weighing just 9 grams, in slightly less than two weeks. And that was only after they melted down the bottle into a "plastic puck."
If you took a little tub of this enzyme, which they used to break down the one bottle, and applied it to the whole global plastic problem, it would take about 350 billion years to break down all the PET plastic produced in one year. Building factories and placing this enzyme in great big vats will help scale the technology, perhaps a million-fold or more, but will that make a dent?
The sheer scale of solutions that are needed to curb the plastic waste manufactured each year — let alone remove all the plastic already in the ocean and on the land — is too astronomical to comprehend.
This enzyme’s greatest service, I think, will be in more localized plastic recycling. In the final experiment of the study, the researchers degraded plastic with the new enzyme and recovered the monomers with a yield of 94.9 percent. Perhaps specific factories hoping to offset their waste could use this enzyme to recycle their plastic on a smaller scale.
Until next time,
— Niko // @NikoMcCarty
Email: niko@codonmag.com